Haskel Gas Booster Pressure Test
gregory.wallace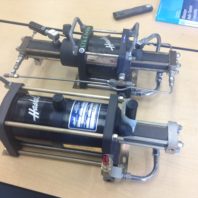
Of the two gas boosters (compressors) we have, we have successfully pressure tested one of them. The Haskel AGD-15 has been tested for stall pressure using nitrogen. This gas booster is a double acting, single state mechanism used to compress a gas to high pressure with only compressed air as a power source.
Our building’s compressed air was used to drive the unit at 90psi. The nitrogen inlet pressure was at 70psi. The nitrogen outlet was a high-pressure pipe connected to a vent valve and a pressure gauge. To test for stall pressure, we left the outlet valve closed. After only a few seconds, we were able to achieve 1400psi at the gauge (expected stall pressure was 1420psi). This implies that the flow rate will be similar to expected when not pumping to stall. However, the output pressure fluctuated significantly: the device would pump once and get to stall pressure. Then it would pause and the pressure would drop to about 1100psi. At this point it would pump again up to 1400psi. This was in part due to the building’s air supply having inadequate flow. Whenever the gas booster pumped, the building air pressure would drop down to 60 or 70 psi and struggle to rise again.
Further testing will require a larger air compressor unit. Now, we need to find whatever is leaking in our gas booster (probably the one-way valves which are quite old). We will also prepare to test our Haskel AG-152 model which has a stall pressure of 13,500psi.

Update: August 24, 2016
Using soapy water, we have leak-tested the AGD-15’s components while running nitrogen gas. Several obvious leaks were fixed, allowing the outlet pressure to rise even further. We managed to get to 1500psi using 90psi air, slightly higher than the expected stall pressure (1420psi). This may be due to the fluctuating air pressure of the supply which may have risen past 90psi. The outlet pressure remained stable when the compressor stalled, which is a great improvement to the previous experiment where gas was clearly leaking.
We also installed an air tank as a buffer between the building’s compressed air lines and the gas booster. This was intended to mediate the problems caused by the fluctuating air supply. But the pressure could only rise to about 1000psi this time. This is either due to higher resistance in the air-flow or because our compressor was started off cold and may require time to “warm up” before operating at full potential. We will probably not use this tank for the experiment.
The AGD-15 compressor system is now fully ready to be installed for the nitrogen liquefaction testing. The other compressor will be tested for stall pressure, afterwards.